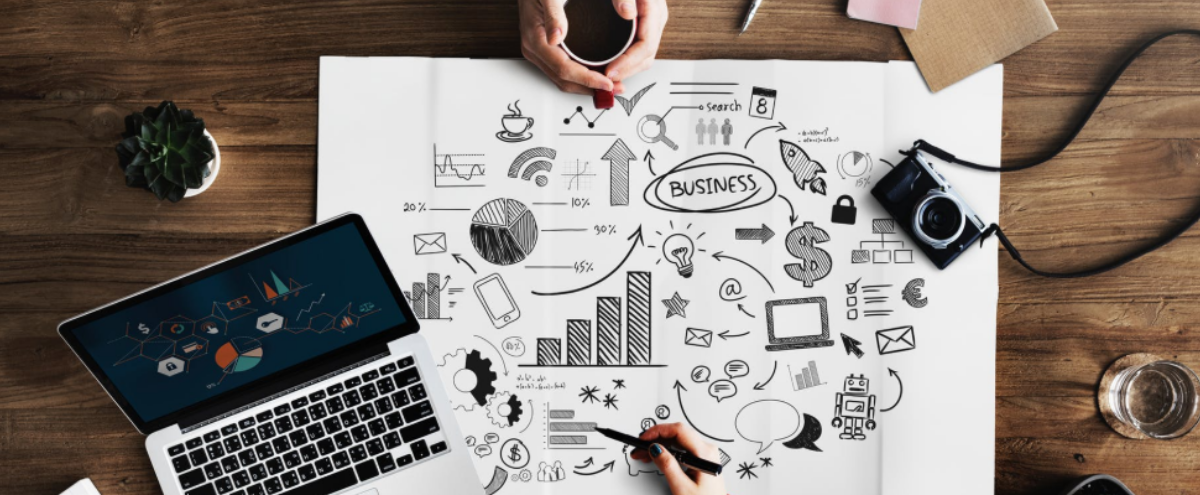
12 Apr The Hands-On Guide to Improve Your Workplace Safety
A safe and healthy workplace not only protects workers from injury and illness, it can also reduce absenteeism and turnover, increase productivity and quality and raise employee morale.
Whether you work at a business, manage it, or own it, you all have the same goal – you do not want anyone to get hurt on the job.
Unfortunately, situations change over time, sometimes even very quickly, making it difficult to identify and control hazards. With hazards comes workplace accidents. Injuries and incidents can happen to anyone, which is why workers have the right to a safe work environment.
There is something that each of you can do to make sure you and your coworkers all go home the same way you started the day. One step at a time, you can make our workplace a better and safer place to work.
Get on Board
Everyone has a role in safety.
For instance, under the Occupational Health and Safety Act (OHSA), employers have a responsibility to provide a safe workplace. As a worker, you have the responsibility of making sure you and your co-workers stay healthy and safe on the job. As an employee, you must be alert and report hazards immediately to a supervisor or employer.
When it comes to creating a culture of safety at work, the right training procedures can make a world of difference.
The Safety Culture Maturity model can help you choose and implement the correct behavioral interventions for your organization:
If you are planning to evaluate your organization’s safety culture you should always ask the opinion of the employees. You must get workers on-board with your safety strategy for it to be successfully implemented.
One of the best ways to motivate workers to get on-board with a safety strategy is to give them a say in a safety program that affects them personally.
Another approach to better motivate workers to participate in safety programs is when they can influence or lead the improvement of safety measures.
The action plan that follows can be focused on organizational changes and training programs.
An important aspect of an action plan to promote a positive health and safety culture is continuous education.
Once responsibilities are developed, all staff must be engaged to develop co-operation and commitment to improving safety. As stated previously, everyone has a role in improving the health and safety of an organization.
It is important to establish objectives and targets around the safety performance within your workplace to measure continuous improvement.
And remember, improving the health and safety culture of your organization is not a one-time effort; continuous improvement is necessary to keep your workplace injury free.
Review these 4 fun ways to get your employees on board with creating a safe and healthy work environment:
- Schedule “Toolbox Talks”
- Provide a suggestion box
- Rally the Team for PPE of the Month
- Add a safety board to your workplace
To have a continuous understanding of the potential harms within your workplace, you must take the time to educate yourself and get in the know.
Get in the Know
You need to be aware of the hazards.
A hazard is anything in the workplace that could hurt you or the people you work with. Examples of common workplace hazards include repetitive movements over and over, slips, trips, and falls, and workplace violence, among many others.
You also need to be aware of less visible hazards related to your work. These hazards could include chemicals, fumes, and toxic dust.
At the root of each work-related injury or illness, there is a hazard. To have a proactive approach in keeping yourself and other employees safe in the workplace, you must have knowledge about the hazards before the workday starts.
Employers, supervisors, and workers need to communicate and work together to make the workplace safer.
- It’s the employer’s duty to make sure that the supervisor knows enough and has enough experience and training to keep workers safe and healthy while they work.
- It’s the employer’s and supervisors duty to inform workers of health and safety hazards.
- It’s the worker’s duty to report known hazards to the supervisor or employer as soon as possible so they can fix the problem.
Effectively communicating between each level of an organization is necessary to control risk. Organizations need to communicate information to their workers on the hazards identified in their risk assessments and on preventive and protective measures.
The best way to protect yourself and those you work with is to identify, manage and take reasonable steps to prevent their potential to harm others.
There are numerous ways to prevent potential harm but the most important item that minimizes risks to acceptable levels is the use of personal protective equipment (PPE).
You can replace a glove, safety glasses, or any other piece of equipment, but you cannot replace an employee. Because accidents occur in a split second, personal protective equipment could potentially save a life.
Personal protective equipment (PPE) is defined as the protective clothing designed to protect the wearer’s body from injury or infection. They are worn to minimize exposure to risks and are designed to protect you where you are vulnerable – eyes, hands, and feet.
Protective clothing should be chosen for the specific work activity and can include: helmets, goggles, or other garments or equipment.
The hazards addressed by protective equipment include physical, electrical, heat, chemicals, biohazards, and airborne particulate matter.
OSHA strictly regulates employers to provide their employees with proper PPE. In some cases, however, accidents occur not because of “absence or lack of” PPE, but because employees choose not to wear it.
An employer is required to train each worker that is required to use personal protective equipment to know the following:
- When it is necessary
- What kind is necessary
- How to properly put it on, adjust, wear and take off
- The limitations of the equipment
- Proper care, maintenance, useful life, and disposal of the equipment
If PPE is used in the workplace, a PPE program should be implemented.
The program should address the potential workplace hazards, the selection, maintenance and use of PPE, the training of employees, and continuous monitoring of the program to ensure its ongoing effectiveness.
You can never know too much. It is best to educate yourself on the potential hazards that your environment or actions pose to yourself or others.
It is all about knowing the health and safety duties of employers, supervisors, and the duties and right of workers, and putting them into action.
We all have to get involved.
Get Involved
To be effective, any safety and health program needs genuine participation from workers and their supervisors.
- An employer must try to eliminate or reduce any hazards, make sure workers are informed about it, and how to deal with it.
- A supervisor must explain all hazards to the workers and how to deal with it.
- A worker must report all identified hazards to the supervisor or the employer.
Full participation means the employer, supervisor, and worker are involved in establishing, operating, evaluating, and improving the safety and health program of their workplace.
Remember that worker participation is vital to the success of safety and health programs.
Prevention starts by paying attention to details and by following OHSA and the workplace health and safety procedures.
Occupational Health and Safety Act (OHSA) gives you the right to participate and get involved in keeping your workplace safe and healthy. There are many ways to do so.
Among others, here are 4 easy ways to get involved in keeping your workplace safe:
- Ask questions when you are unsure about something
- Volunteer to become a health and safety representative or a member of the safety committee
- Help your health and safety representative or safety committee with health and safety inspections by pointing out possible hazards in your workspace
- Take your health and safety training seriously and put what you learn into practice
Unfortunately, in some workplaces, safety is not of high priority and does not receive much attention. If you have felt this way in a past job, you are not alone.
Help is always available from outside the workplace.
Get More Help
You can never know too much. It is best to educate yourself on the potential hazards that your environment or actions pose to yourself or others. Often, you must find resources that are outside of the workplace.
First, you should know your rights.
Remember we mentioned this before? If you are aware of an unsafe work environment or see anything hazardous, it is your right to report it your supervisor or employee.
You also have the right to refuse unsafe work. If you have reason to believe that the work you are doing or the equipment you are using might hurt you or others in the workplace, you have the right to refuse work. You should never engage in a dangerous workspace.
Next, if you believe working conditions are unsafe or unhealthy, you may file a confidential complaint with OSHA and ask for an inspection. OSHA advises that if possible, bring the conditions to your employer’s attention.
How to File a Safety and Health Complaint: https://www.osha.gov/workers/file_complaint.html
Lastly, it is illegal for an employer to fire, demote, transfer or otherwise retaliate against a worker for using their rights under the law. If you believe you have been retaliated against in any way, file a whistle-blower complaint within 30 days of the alleged retaliation.
How to File a Whistle-Blower Complaint: https://www.whistleblowers.gov/complaint_page
If you have any additional questions about a health and safety issue at your workplace, your rights or to learn more about OSHA, they can be reached by phone, email or appointment.
How to Contact OSHA: https://www.osha.gov/workers/
Knowing your health and safety rights and duties of the employer, supervisor, and employee is an important first step in staying safe on the job.
For additional information and resources, keep reading.
Additional Information & Resources
The health and safety culture change of any workplace is not achieved quickly and plans to improve an existing culture should take into account that it will have evolved over a long period of time.
Below are additional resources to begin a culture shift towards improved safety and accountability.
EHS Today
Source for environment, health, and safety best management practices including workplace
safety, OSHA and industrial safety and hygiene.
https://www.ehstoday.com/
216.696.7000
National Safety Council
Nonprofit, public service organization promoting health and safety.
https://www.nsc.org/
800.621.7619
Occupational Safety and Health Administration
Provides training, outreach, education and assistance.
https://www.osha.gov
800-321-6742 (OSHA)
Toolbox Talks
Informal group that focuses on particular safety issues. These tools can be used daily to promote department safety culture as well as to facilitate health and safety discussion on job sites.
https://www.ehs.harvard.edu/programs/toolbox-talks
ehs@harvard.edu
Works Cited
file://hd01/GIA-Profiles/rstoyer/Downloads/Promoting%20a%20positive%20culture.pdf
https://en.wikipedia.org/wiki/Personal_protective_equipment
https://www.dol.gov/
https://www.healthandsafetyhandbook.com.au/do-this-to-get-workers-on-board-with-your-safety-strategy/
https://www.nsc.org/work-safety/tools-resources/infographics/workplace-injuries
https://www.osha.gov/shpguidelines/worker-participation.html
https://www.osha.gov/workers/
No Comments